Leading Indicators - Control Loops
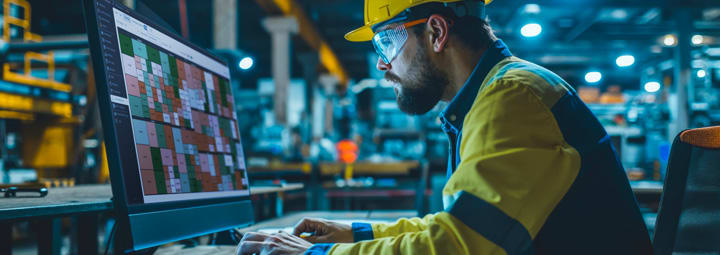
The development of control loops revolutionized industrial processes. Control loops transform the way processes work and directly impact productivity, quality and safety. A facility with well-performing control loops produces a highly consistent, quality product with minimal need for operators to intervene in the process. In turn, this improves equipment reliability by reducing cycles and swings on the equipment.
A control loop monitors a condition in the process, such as temperature, pressure, flow, level, etc. (process value), and then compares that value to the desired target (setpoint). The control loop continues to calculate and implement adjustments to equipment in the field such as valve position, motor speed, etc. (output). The purpose of the control loop is twofold. Firstly, to ensure the process condition is maintained around the setpoint - dependent on the design intent of the loop. Secondly, to return the process to normal operating conditions if a disturbance or upset was introduced into the process.
When an upset occurs, the automatic control loops are the first line of defense to handle this and return the process back to normal, optimal conditions. Rejecting the disturbance in the process with the control loop prevents escalation to the next layer of protection - the alarm and operator response. Addressing process issues before they escalate through different layers of protection is key to improving overall operations.
As a first layer of protection, control loops are a good source of leading indicators of process safety performance. Here are some of the metrics we’ve found to be beneficial in understanding the performance of this layer of protection:
-
Number of loops in manual – Control loops are only effective if they actively monitor the process and adjust the outputs. A control loop in manual mode is an open loop that does not control the process. If it’s not controlling the process, it’s not maintaining the setpoint nor rejecting disturbances. A loop in manual effectively bypasses any benefits of the loop. Incorporating the list of loops in manual into shift handovers is a great way to inform incoming operators of what areas may need additional oversight and maintain focus on the problem.
-
Percentage of time a loop spends in manual – Similar to the total number of loops in manual, understanding how long a loop spends in manual when it should be controlling the process is a good indicator of its performance and the management systems in place to address chronic issues with control loops.
-
Composite metrics and indices:
-
-
Stability index – A stability index is a measure of a loop’s tendency to oscillate. Oscillations induce cyclic behavior in a loop, increasing variation, the likelihood of disturbances downstream and equipment wear and tear, all leading to other problems later.
-
Response index – A response index is a measure of the loop's ability to maintain a setpoint. Note that this measure is dependent on the design intent of the loop. As such, it should be adjustable per loop to meet the design requirements, whether it be tight control to a setpoint or a defined smooth response to prevent passing the disturbance downstream and inducing other potential issues.
-
Service index – A service index is an operator-centric view of the loop's performance. If it spends a lot of time in manual, it probably doesn’t work very well. If the loop generates many alarms, or has many operator changes like mode, setpoint and output changes, it probably doesn’t behave well.
-
Control loop performance index – An overall control loop performance index is the lowest of the three metrics listed above. A weighted control loop performance index enables high-level performance reporting over many loops where the weights of each loop’s sub-index are tailored to the purpose of the loop.
-
Monitoring the performance of leading indicators enables you to uncover and address issues before they have a chance to escalate to the next layer of protection - or more serious lagging indicators like shutdowns, evacuations or even worse scenarios.
For additional resources, check out: