Why walk it down when you can look it up?
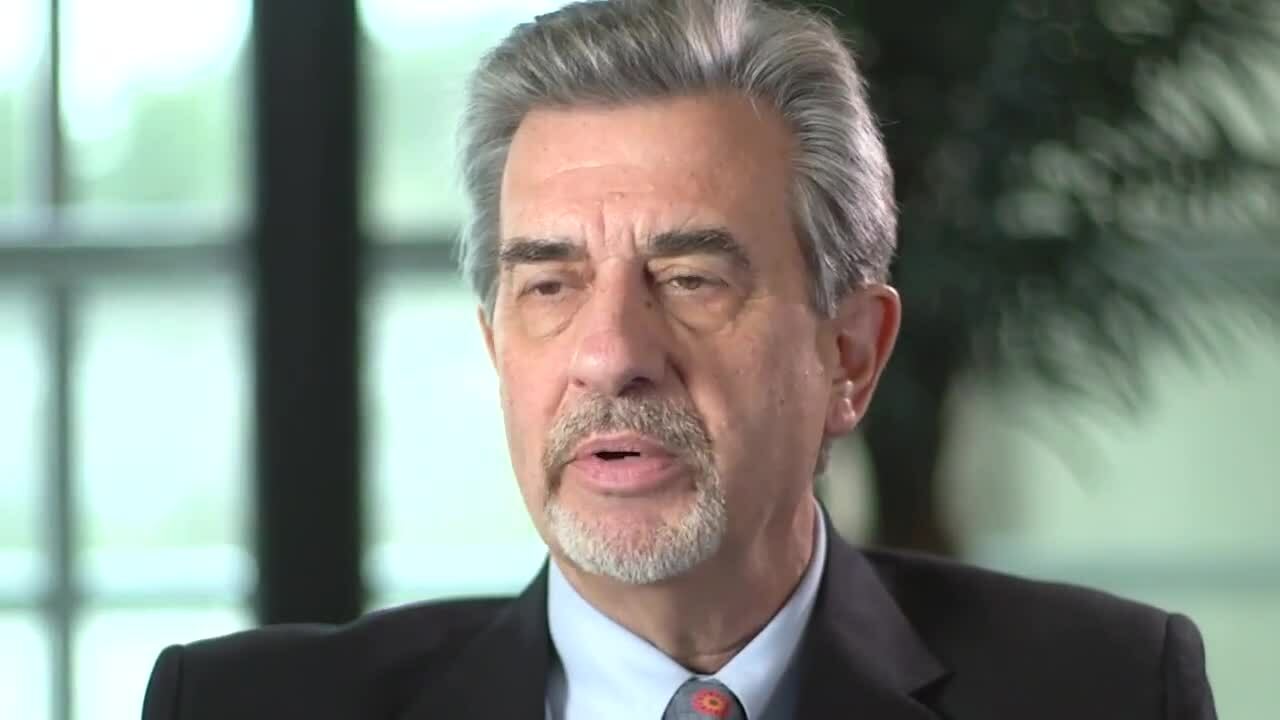
Andrew Gregg of Gregg Valdés & Associates shares his favorite Hexagon PPM implementation (SmartPlant Foundation), which saved weeks of personnel time after a faulty part was discovered. Gregg Valdés & Associates provides specialized engineering document and data management services for the oil and gas industry, from development of major capital projects to operations phase and brownfield projects; they and have delivered efficiency benefits which result from easy access to equipment tag data and linking to engineering and vendor documentation." To start your CFIHOS implementation, view our CFIHOS handover specifications here: http://bit.ly/HandoverSpecs *** I do have a favorite handover success story. Going back to the assembly of information from projects to operations using S.P.F. at the time. It was interesting in that we had some difficulty educating managers in what this was about. But when we took the project down and presented to the people working inside, the operations representatives working on site, we arranged a 20-minute presentation. They stopped us after 5 minutes and said, “We get it, and we’d like it as soon as possible." So it’s much easier to enroll the engineers, who had either worked with it, could understand it, then it was to enroll the managers. But I guess the success story is that within a week of operation of that particular asset they discovered they had a level gauge that was a bad actor. But the important piece was they come back to us and said, “We’ve found one that’s faulty, but we know we have others, so, can you tell us where they are?” And we were able to tell them within a space of 5 minutes, using SPF, we could look up the model number, we could find the locations and tell them that they had 52 of these level gauges that really had to be fixed urgently. I think both the engineers who had to do the fix, plus the management was very impressed with the speed of turnaround. At the time, I think they were saying it could have taken a couple of weeks to go scour the documents, trying to find out where level gauges were installed and then trying to ensure they were worked out, which of the level gauges was this particular model. It could have been multiple weeks of a couple of people chasing down this information. Probably done by people off-shore who really shouldn’t be spending their efforts in that activity and extremely expensive when they’re sitting offshore. So I think we significantly reduced the administrative effort that the offshore people had to go through to find information about their facility and to cross-relate the models, the tags, and the equipment they had offshore.